Strategic Cost Reduction: How to Optimize Expenses Without Sacrificing Quality
“In today's competitive business landscape, strategic cost reduction has become essential for maintaining profitability and operational efficiency. This comprehensive guide explores effective approaches to reduce expenses without compromising quality, covering everything from technology optimization to process improvement and sustainable practices that deliver long-term value. ”

Strategic Cost Reduction: How to Optimize Expenses Without Sacrificing Quality
In today's competitive business environment, organizations across all industries face increasing pressure to do more with less. Strategic cost reduction has become a critical component of business success, allowing companies to maintain profitability while navigating economic uncertainties. However, effective cost reduction isn't simply about cutting expenses—it's about optimizing spending to create sustainable value.
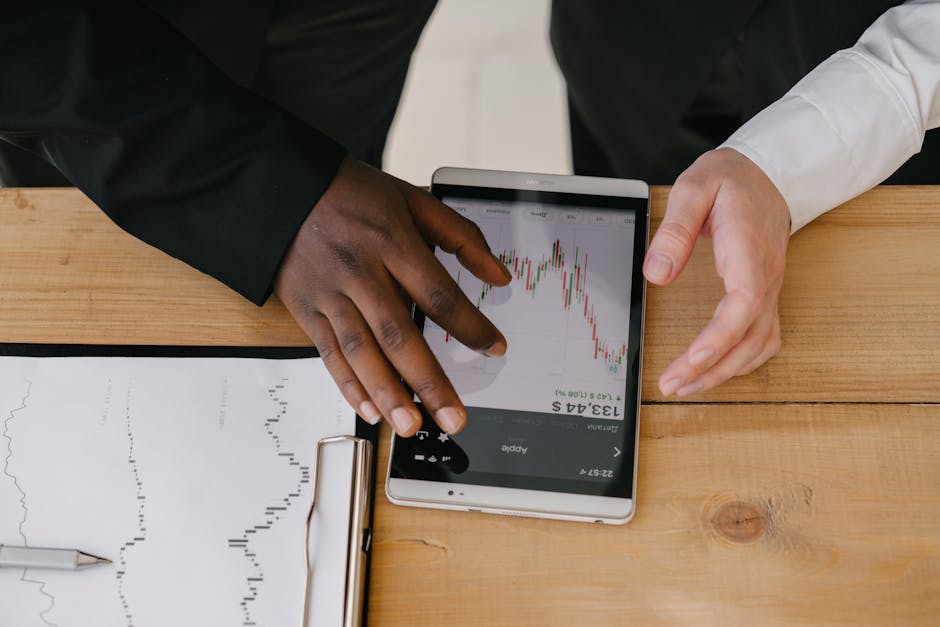
Understanding Strategic Cost Reduction
Strategic cost reduction differs from traditional cost-cutting measures in its approach and objectives. While conventional cost-cutting often involves across-the-board reductions that can harm operational capabilities, strategic cost reduction focuses on identifying and eliminating inefficiencies while preserving or even enhancing core business functions.
The goal is to create a leaner, more agile organization that can respond effectively to market changes while maintaining high-quality products and services. This approach requires a comprehensive understanding of your organization's cost structure and value chain.
Benefits of Strategic Cost Reduction
When implemented effectively, strategic cost reduction offers numerous advantages:
- Improved profitability: By reducing unnecessary expenses, organizations can increase their bottom line without sacrificing quality or growth potential.
- Enhanced competitiveness: Lower operating costs can enable more competitive pricing or increased investment in innovation and customer experience.
- Greater operational efficiency: The process of analyzing costs often reveals inefficiencies and opportunities for process improvement.
- Increased business resilience: Organizations with optimized cost structures are better positioned to weather economic downturns and market disruptions.
Key Strategies for Effective Cost Reduction
1. Technology Optimization and Automation
One of the most impactful approaches to cost reduction involves leveraging technology to streamline operations and reduce manual effort. According to IBM's Cost of Data Breach 2024 Report, organizations that deployed AI-enabled security tools and automation extensively saw a USD 2.2 million lower average cost per breach compared to organizations with no AI deployed.
Consider these technology-focused cost reduction strategies:
- Cloud migration: Moving from on-premises infrastructure to cloud computing can significantly reduce capital expenditures and maintenance costs while providing scalability and flexibility.
- Process automation: Implementing robotic process automation (RPA) for routine, rule-based tasks can reduce labor costs and minimize errors.
- AI and machine learning: Advanced analytics and artificial intelligence solutions can optimize operations, predict maintenance needs, and identify cost-saving opportunities that humans might miss.
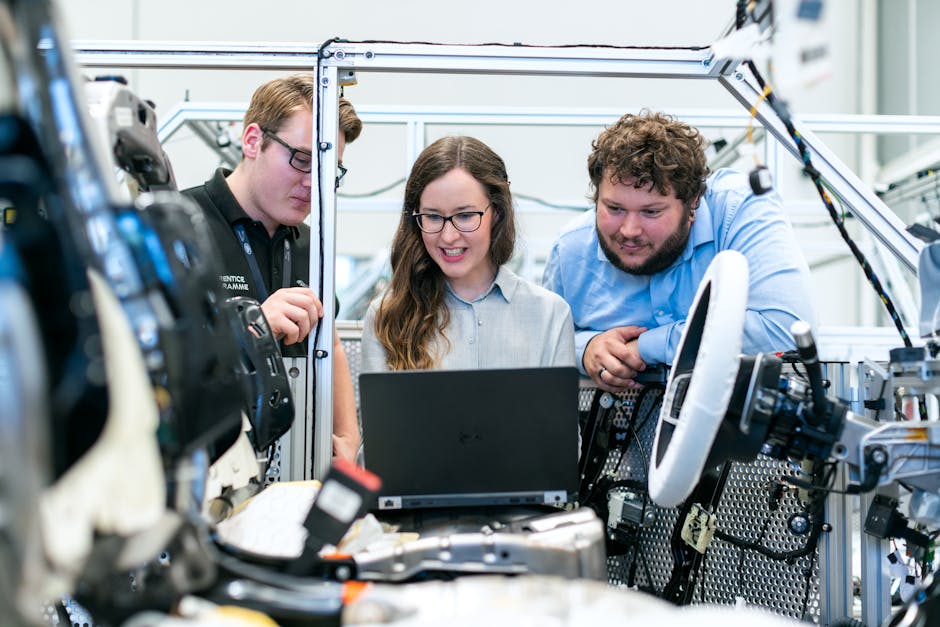
2. Workplace and Real Estate Optimization
For many organizations, real estate and workplace costs represent a significant portion of operating expenses. The rise of remote and hybrid work models has created new opportunities for office space optimization:
- Hybrid workplace models: Implementing flexible work arrangements can reduce office space requirements and associated costs.
- Space utilization analysis: Using occupancy data to right-size your real estate footprint can eliminate waste while ensuring employees have the spaces they need.
- Energy efficiency improvements: Investing in energy-efficient systems and sustainable building practices can reduce utility costs while supporting environmental goals.
3. Supply Chain and Procurement Optimization
The supply chain represents another major area for potential cost savings:
- Vendor consolidation: Reducing the number of suppliers can increase purchasing power and reduce administrative costs.
- Strategic sourcing: Implementing competitive bidding processes and negotiating volume-based discounts can lower procurement costs.
- Inventory optimization: Using data analytics to maintain optimal inventory levels can reduce carrying costs while ensuring product availability.
4. Process Improvement and Waste Reduction
Inefficient processes waste resources and increase costs. Implementing methodologies like Lean and Six Sigma can help identify and eliminate these inefficiencies:
- Value stream mapping: Analyzing workflows to identify non-value-adding activities that can be eliminated.
- Standardization: Creating consistent processes reduces errors, rework, and associated costs.
- Continuous improvement culture: Empowering employees to identify and address inefficiencies can create ongoing cost savings.
Implementing a Strategic Cost Reduction Initiative
Successful cost reduction requires a structured approach and organizational commitment. Here's a framework for implementing an effective initiative:
1. Establish Clear Objectives and Metrics
Begin by defining specific, measurable goals for your cost reduction efforts. These might include:
- Percentage reduction in specific expense categories
- Improvement in key financial ratios
- Enhanced productivity metrics
- Customer satisfaction targets
Having clear metrics allows you to track progress and demonstrate the value of your initiatives to stakeholders.
2. Conduct a Comprehensive Cost Analysis
Before making any changes, thoroughly analyze your current cost structure:
- Activity-based costing: Understand the true costs of different activities and processes.
- Benchmarking: Compare your costs against industry standards to identify areas where you may be spending more than necessary.
- Cost driver analysis: Identify the factors that influence your major expense categories.
This analysis will help you prioritize opportunities with the greatest potential impact.
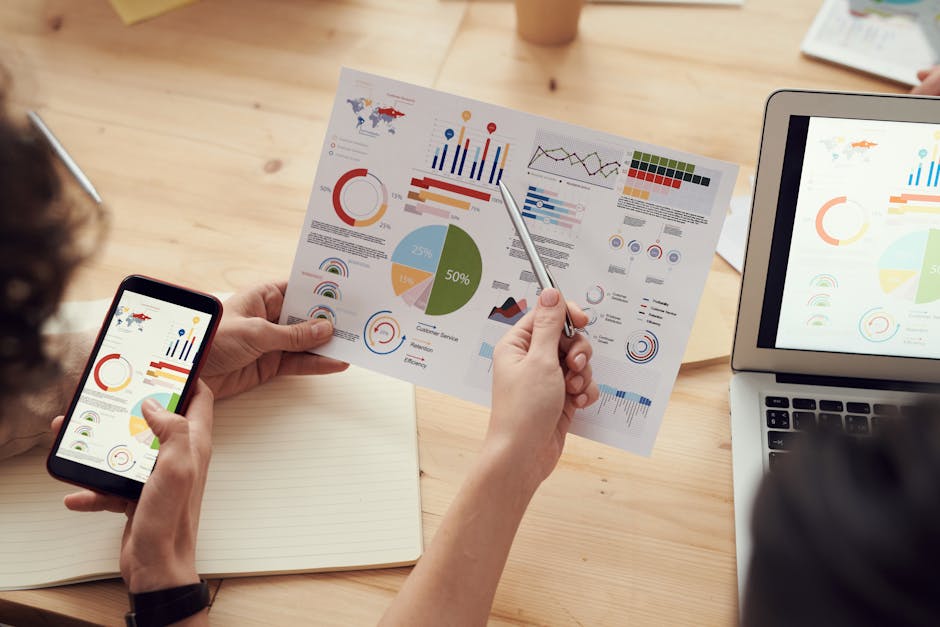
3. Develop a Balanced Portfolio of Initiatives
Create a mix of short-term and long-term cost reduction initiatives:
- Quick wins: Identify immediate savings opportunities that can be implemented with minimal investment or disruption.
- Strategic initiatives: Develop longer-term projects that may require investment but offer substantial ongoing savings.
- Capability-building efforts: Invest in training and tools that enable continuous cost optimization.
4. Engage Stakeholders and Build Support
Cost reduction efforts often face resistance. To overcome this:
- Communicate the vision: Clearly explain why cost reduction is necessary and how it will benefit the organization and its stakeholders.
- Involve employees: Engage front-line staff in identifying opportunities and developing solutions.
- Celebrate successes: Recognize and reward cost-saving innovations to reinforce the desired behaviors.
5. Monitor Results and Adjust as Needed
Implement robust tracking mechanisms to:
- Measure the actual impact of each initiative
- Identify any unintended consequences
- Make adjustments to maximize results
- Share outcomes with stakeholders
Common Pitfalls to Avoid
Even well-intentioned cost reduction efforts can go awry. Watch out for these common mistakes:
1. Across-the-Board Cuts
Mandating the same percentage reduction for all departments ignores the unique value and efficiency of different functions. This approach often leads to cuts in areas that directly impact customer satisfaction or revenue generation.
2. Focusing Solely on Short-Term Savings
Prioritizing immediate cost reductions without considering long-term implications can damage capabilities and ultimately increase costs. For example, deferring maintenance might save money today but lead to expensive equipment failures later.
3. Neglecting Customer Impact
Cost-cutting measures that negatively affect the customer experience can reduce loyalty and revenue, offsetting any savings. Always evaluate potential customer impacts before implementing changes.
4. Failing to Address Root Causes
Treating symptoms rather than underlying issues provides only temporary relief. For sustainable cost reduction, identify and address the root causes of inefficiency and waste.
Sustainable Cost Reduction Through Technology
Modern technology offers powerful tools for sustainable cost reduction. Here are some specific applications:
Data Analytics for Informed Decision-Making
Data analytics provides insights that can guide cost optimization efforts:
- Predictive maintenance: Using sensor data and machine learning to perform maintenance only when needed, reducing both maintenance costs and downtime.
- Customer behavior analysis: Understanding customer preferences to optimize product offerings and marketing spend.
- Process mining: Analyzing system logs to identify inefficiencies in business processes.
Digital Transformation for Operational Efficiency
Digital transformation initiatives can fundamentally change how work gets done:
- Paperless processes: Eliminating paper-based workflows reduces material costs, storage requirements, and processing time.
- Self-service capabilities: Enabling customers and employees to handle routine tasks independently reduces support costs.
- Remote collaboration tools: Supporting effective teamwork regardless of location reduces travel expenses and office space requirements.
IoT and Smart Building Technology
The Internet of Things (IoT) enables significant facility-related cost savings:
- Smart lighting and HVAC: Automatically adjusting lighting and temperature based on occupancy and time of day reduces energy consumption.
- Predictive maintenance for building systems: Using sensors to monitor equipment performance and predict failures before they occur.
- Space utilization monitoring: Collecting data on how spaces are actually used to inform real estate decisions.
Case Studies: Successful Cost Reduction Initiatives
Manufacturing Company: Process Optimization
A mid-sized manufacturing company implemented a Lean Six Sigma program focused on reducing waste in production processes. By analyzing value streams and implementing standardized work procedures, they:
- Reduced raw material waste by 15%
- Decreased production cycle time by 22%
- Lowered overall manufacturing costs by 12%
The key to their success was engaging front-line employees in identifying and solving problems, creating a culture of continuous improvement.
Financial Services Firm: Technology Consolidation
A financial services organization discovered they were using multiple overlapping software platforms for similar functions. Through a systematic review and consolidation effort, they:
- Reduced software licensing costs by $1.2 million annually
- Decreased IT support requirements by 18%
- Improved system integration, reducing manual data entry and associated errors
Their approach included forming cross-functional teams to evaluate business needs and select the best solutions, ensuring that cost reduction didn't compromise functionality.
Healthcare Provider: Energy Efficiency
A hospital network implemented a comprehensive energy management program that included:
- Upgrading to LED lighting throughout facilities
- Installing smart building controls
- Optimizing HVAC systems
- Implementing water conservation measures
These initiatives reduced utility costs by over $3 million annually while improving comfort for patients and staff. The project paid for itself in less than three years and continues to generate savings.
Conclusion: Building a Cost-Conscious Culture
The most successful organizations view cost optimization not as a one-time project but as an ongoing discipline. Building a cost-conscious culture involves:
- Leadership commitment: Executives must model cost-conscious behaviors and decision-making.
- Employee empowerment: Front-line staff should be encouraged to identify and address inefficiencies.
- Performance management: Cost metrics should be incorporated into goals and evaluations at all levels.
- Continuous learning: Organizations should regularly benchmark and adopt best practices for cost optimization.
By approaching cost reduction strategically and embedding it in your organizational culture, you can create sustainable competitive advantage while maintaining the capabilities needed for long-term success.
Remember that effective cost reduction isn't about doing less—it's about doing more with less, eliminating waste while preserving and enhancing the activities that create value for customers and stakeholders.