Quality Assurance: Building a Foundation for Excellence in the Modern Workplace
“Quality assurance is more than just checking boxes—it's a strategic approach that can transform your organization's performance. This comprehensive guide explores how QA processes improve product quality, enhance customer satisfaction, and drive business growth through systematic prevention of defects and continuous improvement. ”

Understanding Quality Assurance in the Modern Workplace
Quality Assurance (QA) is a systematic approach that determines if a product or service meets specific requirements and specifications. Unlike quality control, which focuses on identifying defects after they occur, quality assurance is proactive—it's about preventing quality issues before they happen by establishing standards, guidelines, and procedures that maintain the integrity of products and services throughout their development.
In today's competitive business landscape, quality assurance has become a critical component of organizational success. It increases customer confidence, enhances a company's credibility, and improves work processes and efficiency. When implemented effectively, QA also helps companies compete more successfully in their markets.
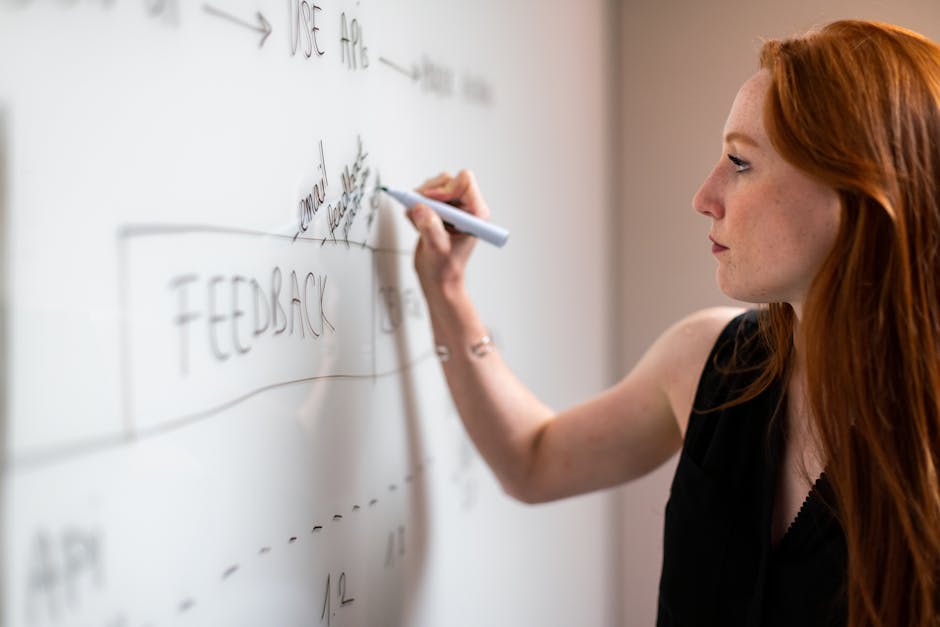
The Strategic Value of Quality Assurance
Quality assurance isn't just about checking boxes; it's a strategic investment that delivers significant business benefits:
Building Customer Trust and Loyalty
The quality assurance process helps businesses ensure their products meet the quality standards set by the company or industry. This consistency builds trust with customers, who come to rely on the predictable excellence of your offerings. Many businesses view their QA program as a promise to both internal stakeholders and customers that the company will deliver high-quality products that provide a positive user experience.
Reducing Costs Through Prevention
By identifying and addressing potential issues early in the development process, quality assurance helps organizations avoid costly rework, warranty claims, and customer support issues. According to industry studies, the cost of fixing a defect increases exponentially the later it's discovered in the development lifecycle. Implementing robust QA processes can significantly reduce these costs.
Enhancing Operational Efficiency
Quality assurance promotes standardization and best practices across an organization, leading to more efficient operations. By documenting processes and establishing clear guidelines, QA helps eliminate redundancies, reduce waste, and streamline workflows. This not only improves productivity but also creates a more consistent and predictable work environment.
Key Components of an Effective Quality Assurance System
A comprehensive quality assurance system typically includes several key components:
Quality Planning
Quality planning involves setting quality objectives and specifying the operational processes and resources needed to fulfill these objectives. This includes:
- Defining quality standards and metrics
- Establishing quality policies and procedures
- Identifying required resources and training needs
- Setting up quality control checkpoints
Quality Control
While quality assurance focuses on preventing defects, quality control is about identifying and correcting defects that do occur. An effective QA system incorporates quality control activities such as:
- Inspections and testing
- Statistical sampling
- Defect tracking and analysis
- Corrective action processes
Quality Improvement
Continuous improvement is at the heart of quality assurance. This involves:
- Regularly reviewing quality metrics and performance data
- Identifying opportunities for improvement
- Implementing changes to enhance quality
- Monitoring the effectiveness of improvements
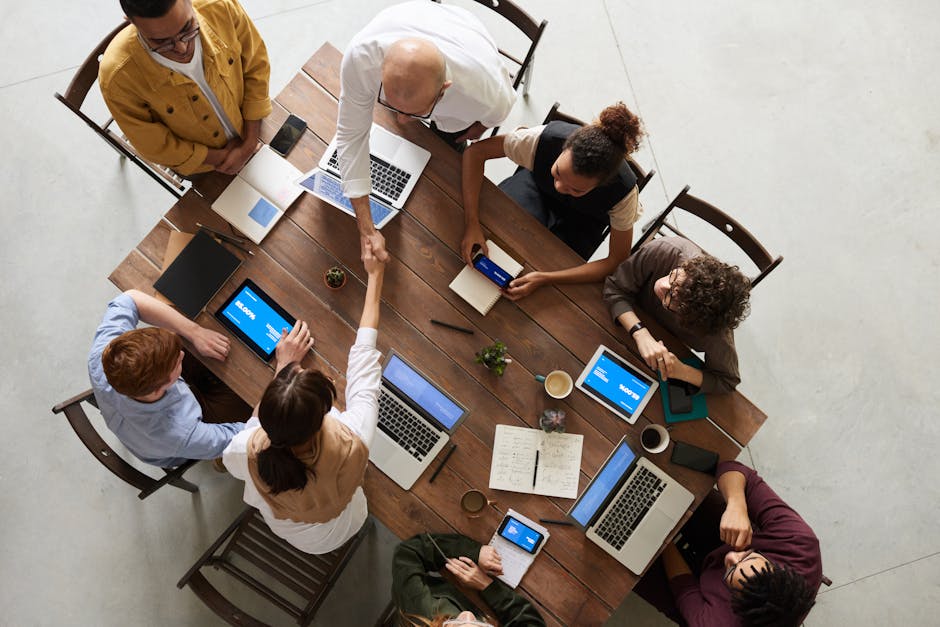
Quality Assurance Methodologies and Approaches
Several methodologies and approaches can guide your quality assurance efforts:
Total Quality Management (TQM)
Total Quality Management integrates quality assurance into every aspect of a company's operations, encouraging all employees to take ownership of quality and constantly seek ways to enhance processes, reduce waste, and improve product quality. TQM emphasizes customer satisfaction, continuous improvement, and the involvement of all employees in quality initiatives.
Six Sigma
Six Sigma is a data-driven methodology that focuses on minimizing variability in business processes. It uses statistical methods to identify and eliminate defects, with the goal of achieving no more than 3.4 defects per million opportunities. Six Sigma projects follow the DMAIC approach: Define, Measure, Analyze, Improve, and Control.
ISO 9001
ISO 9001 is an internationally recognized standard for quality management systems. It provides a framework for establishing, implementing, maintaining, and improving a quality management system. Organizations can become ISO 9001 certified, demonstrating their commitment to quality and customer satisfaction.
Agile Quality Assurance
In Agile development environments, quality assurance is integrated throughout the development process rather than being a separate phase. This approach emphasizes collaboration, adaptability, and continuous testing, with QA professionals working closely with developers to ensure quality at every stage.
Implementing Quality Assurance in Your Organization
Implementing a quality assurance program requires careful planning and commitment from all levels of the organization:
Step 1: Gain Leadership Support
Quality assurance initiatives need strong support from leadership to succeed. Leaders must understand the value of QA and be willing to invest the necessary resources. They should also model a commitment to quality in their own actions and decisions.
Step 2: Define Quality Standards and Metrics
Clearly define what quality means for your organization and establish metrics to measure it. These standards should align with customer expectations, industry regulations, and organizational goals. They should be specific, measurable, achievable, relevant, and time-bound (SMART).
Step 3: Develop QA Processes and Procedures
Document the processes and procedures that will guide your quality assurance efforts. These should cover all aspects of your operations, from product development to customer service. Make sure these documents are clear, accessible, and regularly updated.
Step 4: Train and Engage Employees
All employees play a role in quality assurance, not just those with "quality" in their job titles. Provide training on quality principles, processes, and tools. Encourage employees to identify quality issues and suggest improvements.
Step 5: Implement QA Tools and Technologies
Invest in tools and technologies that support your quality assurance efforts. These might include testing tools, defect tracking systems, process automation tools, and data analytics platforms. Choose tools that integrate well with your existing systems and are user-friendly.
Step 6: Monitor, Measure, and Improve
Regularly monitor your quality metrics, analyze the data, and use the insights to drive continuous improvement. Celebrate successes and learn from failures. Adjust your QA processes as needed to address changing business needs and customer expectations.
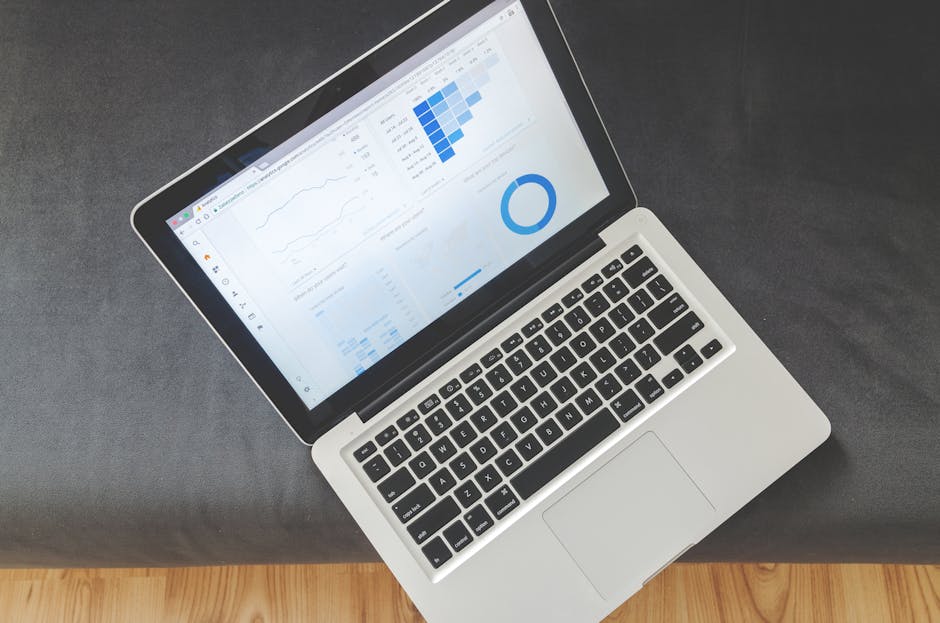
Quality Assurance in Different Industries
While the principles of quality assurance are universal, their application varies across industries:
Manufacturing
In manufacturing, quality assurance focuses on ensuring that products meet specifications and are free from defects. This often involves statistical process control, inspection systems, and compliance with industry standards. Manufacturers may use techniques like Six Sigma and lean manufacturing to improve quality and efficiency.
Software Development
In software development, quality assurance involves testing applications to ensure they meet requirements, are free from bugs, and provide a good user experience. This includes various types of testing, such as unit testing, integration testing, system testing, and user acceptance testing. Agile methodologies often integrate QA throughout the development process.
Healthcare
In healthcare, quality assurance is critical for patient safety and outcomes. It involves adherence to clinical guidelines, infection control protocols, medication safety practices, and continuous monitoring of patient outcomes. Healthcare organizations may use approaches like Plan-Do-Study-Act (PDSA) cycles for quality improvement.
Education
In education, quality assurance focuses on ensuring that educational programs meet accreditation standards and provide valuable learning experiences. This includes curriculum development, faculty evaluation, student assessment, and program review. Educational institutions may use frameworks like the Baldrige Excellence Framework to guide their quality efforts.
The Role of Technology in Quality Assurance
Technology plays an increasingly important role in quality assurance:
Automation
Automation tools can streamline quality assurance processes, reducing human error and freeing up staff for more strategic tasks. Automated testing tools, for example, can quickly and consistently run tests that would be time-consuming to perform manually.
Data Analytics
Data analytics can help organizations identify patterns and trends in quality data, leading to more informed decision-making. By analyzing data from various sources, organizations can identify root causes of quality issues and predict potential problems before they occur.
Artificial Intelligence and Machine Learning
Artificial intelligence and machine learning are transforming quality assurance by enabling more sophisticated analysis and prediction. AI can analyze vast amounts of data to identify patterns that humans might miss, while machine learning algorithms can improve over time, becoming better at predicting quality issues.
Cloud-Based QA Tools
Cloud computing has made sophisticated QA tools more accessible to organizations of all sizes. Cloud-based tools offer scalability, flexibility, and collaboration features that can enhance quality assurance efforts.
Measuring the Success of Your Quality Assurance Program
To determine if your quality assurance program is effective, consider these key performance indicators (KPIs):
Product Quality Metrics
- Defect rate: The number of defects per unit of production
- First-pass yield: The percentage of products that pass inspection without requiring rework
- Customer returns: The rate at which customers return products due to quality issues
- Warranty claims: The frequency and cost of warranty claims
Process Quality Metrics
- Process capability index (Cpk): A measure of how well a process meets specifications
- Cycle time: The time it takes to complete a process
- Rework rate: The percentage of work that must be redone due to quality issues
- Compliance rate: The percentage of processes that adhere to established procedures
Customer Satisfaction Metrics
- Customer satisfaction score (CSAT): A measure of how satisfied customers are with your products or services
- Net Promoter Score (NPS): A measure of how likely customers are to recommend your products or services
- Customer complaints: The frequency and nature of customer complaints
- Customer retention rate: The percentage of customers who continue to do business with you
Case Study: How Quality Assurance Transformed a Business
Let's look at a hypothetical scenario in which robust QA processes can help a business identify and resolve issues quickly, safeguarding both product quality and customer trust.
The Challenge
A mid-sized software company was experiencing an increasing number of customer complaints about bugs in their flagship product. These issues were damaging their reputation and leading to customer churn. The development team was spending more time fixing bugs than developing new features, creating a vicious cycle of reactive firefighting.
The QA Solution
The company implemented a comprehensive quality assurance program that included:
- Establishing clear quality standards and acceptance criteria for all features
- Implementing automated testing for regression testing and routine checks
- Creating a dedicated QA team that worked closely with developers from the start of each project
- Developing a robust bug tracking and prioritization system
- Instituting regular code reviews and pair programming practices
The Results
Within six months, the company saw significant improvements:
- Bug reports decreased by 65%
- Customer satisfaction scores increased by 28%
- Development velocity improved as less time was spent on bug fixes
- The company was able to release new features more frequently and reliably
- Employee morale improved as they took pride in delivering a high-quality product
This case study illustrates how a strategic approach to quality assurance can transform not just product quality but the entire business.
Overcoming Common Quality Assurance Challenges
Implementing and maintaining an effective quality assurance program isn't without challenges:
Resource Constraints
Quality assurance requires an investment of time, money, and personnel. In resource-constrained environments, it can be challenging to secure these investments, especially when the benefits may not be immediately apparent.
Solution: Start small with high-impact QA initiatives that demonstrate quick wins. Use data to show the return on investment from these initiatives, such as reduced rework costs or improved customer satisfaction.
Resistance to Change
Employees may resist new quality assurance processes, seeing them as bureaucratic or questioning the implication that their work isn't already high quality.
Solution: Involve employees in developing QA processes, emphasizing how these processes will make their work easier and more satisfying. Celebrate successes and recognize contributions to quality improvement.
Balancing Quality and Speed
In fast-paced environments, there's often pressure to deliver quickly, which can conflict with thorough quality assurance.
Solution: Integrate QA throughout the development process rather than treating it as a separate phase. Use automation to speed up routine testing. Demonstrate how investing in quality upfront can actually save time by reducing rework.
Maintaining Momentum
Initial enthusiasm for quality initiatives can wane over time, leading to a gradual erosion of QA practices.
Solution: Keep quality visible through regular reporting on quality metrics. Continuously refresh and update QA processes to keep them relevant. Tie quality performance to recognition and rewards.
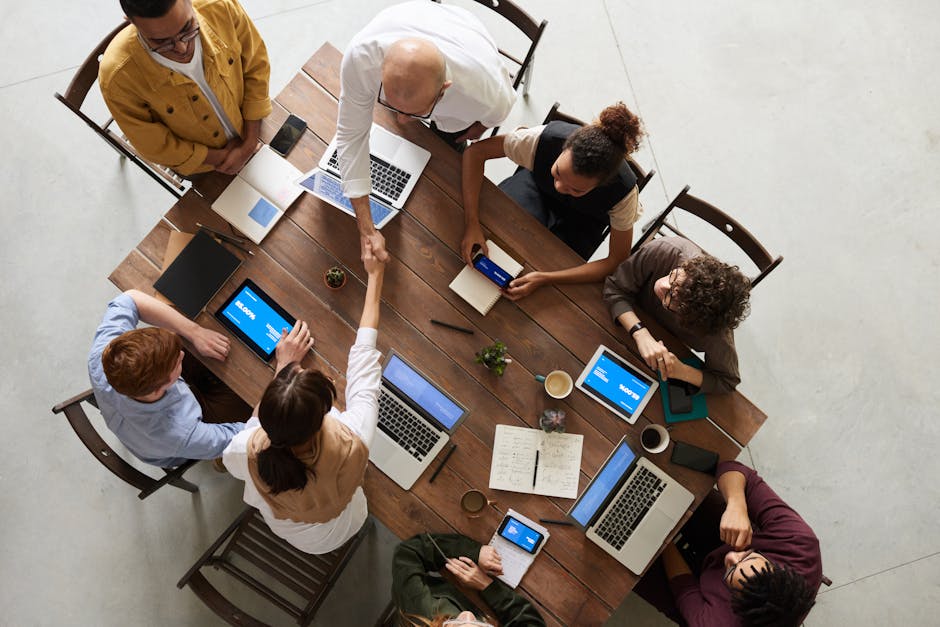
The Future of Quality Assurance
As we look to the future, several trends are shaping the evolution of quality assurance:
Integration of QA and Development
The lines between quality assurance and development are blurring, with more organizations adopting DevOps and continuous integration/continuous deployment (CI/CD) approaches. This integration enables faster feedback loops and more collaborative problem-solving.
Shift-Left Testing
There's a growing emphasis on "shifting left" in the development process, meaning testing and quality assurance activities start earlier. This approach helps identify and address issues when they're less expensive to fix.
AI-Powered Quality Assurance
Artificial intelligence is increasingly being applied to quality assurance, from automated test generation to predictive analytics that can identify potential quality issues before they occur. AI can also help prioritize testing efforts by identifying high-risk areas.
Focus on Customer Experience
Quality assurance is expanding beyond functional requirements to encompass the entire customer experience. This includes usability, accessibility, performance, and emotional response to products and services.
Conclusion: Making Quality Assurance a Competitive Advantage
In today's competitive business environment, quality is a key differentiator. Organizations that excel at quality assurance don't just avoid problems—they create products and services that delight customers, operate efficiently, and adapt quickly to changing needs.
By investing in a robust quality assurance program, you're not just preventing defects; you're building a foundation for excellence that can transform your organization's performance and reputation. Whether you're in manufacturing, software development, healthcare, education, or any other industry, quality assurance provides a framework for continuous improvement and customer satisfaction.
Remember that quality assurance is not a one-time project but an ongoing commitment. It requires leadership support, employee engagement, appropriate tools and technologies, and a culture that values quality. With these elements in place, quality assurance can become a powerful competitive advantage for your organization.
Start by assessing your current quality assurance practices, identifying gaps, and developing a plan to strengthen your approach. Even small improvements can yield significant benefits, creating a virtuous cycle of better quality, higher customer satisfaction, and improved business performance.