Navigating OSHA Regulations: A Comprehensive Guide for Manufacturing Plants
“This article provides a comprehensive overview of OSHA regulations for manufacturing plants, offering insights on compliance strategies, common violations, and best practices for maintaining a safe work environment. Learn how to navigate the complex regulatory landscape and protect your workforce while avoiding costly penalties. ”

Navigating OSHA Regulations: A Comprehensive Guide for Manufacturing Plants
In today's complex regulatory environment, manufacturing plants face the ongoing challenge of staying compliant with Occupational Safety and Health Administration (OSHA) regulations. With an average of 1.5 new manufacturing-related regulations issued each week since 1981, it's crucial for plant managers and safety professionals to stay informed and proactive in their approach to workplace safety.
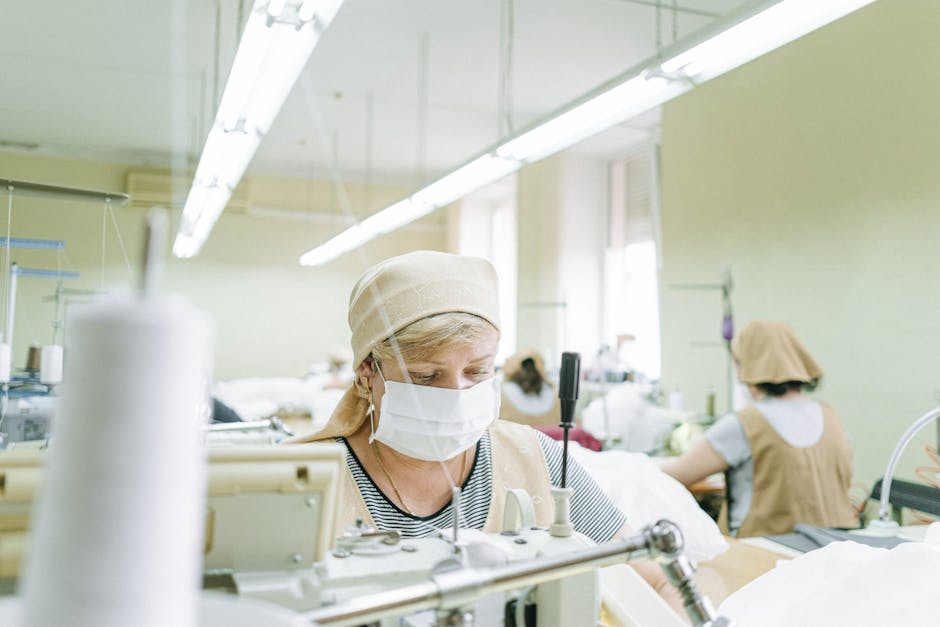
Understanding OSHA's Role in Manufacturing
OSHA, a federal agency operating under the U.S. Department of Labor, sets and enforces workplace safety and health standards. For manufacturing plants, compliance with OSHA regulations is not just a legal requirement but a fundamental aspect of ensuring employee safety and operational efficiency.
Key Areas of OSHA Regulations in Manufacturing
-
Hazard Communication: Manufacturers must maintain safety data sheets (SDS) for all hazardous chemicals and ensure proper labeling and employee training.
-
Machine Guarding: Proper guards must be in place to protect workers from moving machine parts, flying debris, and other potential hazards.
-
Respiratory Protection: When engineering controls are not feasible, appropriate respiratory protection must be provided and properly maintained.
-
Electrical Safety: Compliance with OSHA's electrical standards is crucial to prevent accidents and injuries related to electrical hazards.
-
Lockout/Tagout Procedures: These are essential for controlling hazardous energy during maintenance and servicing of equipment.
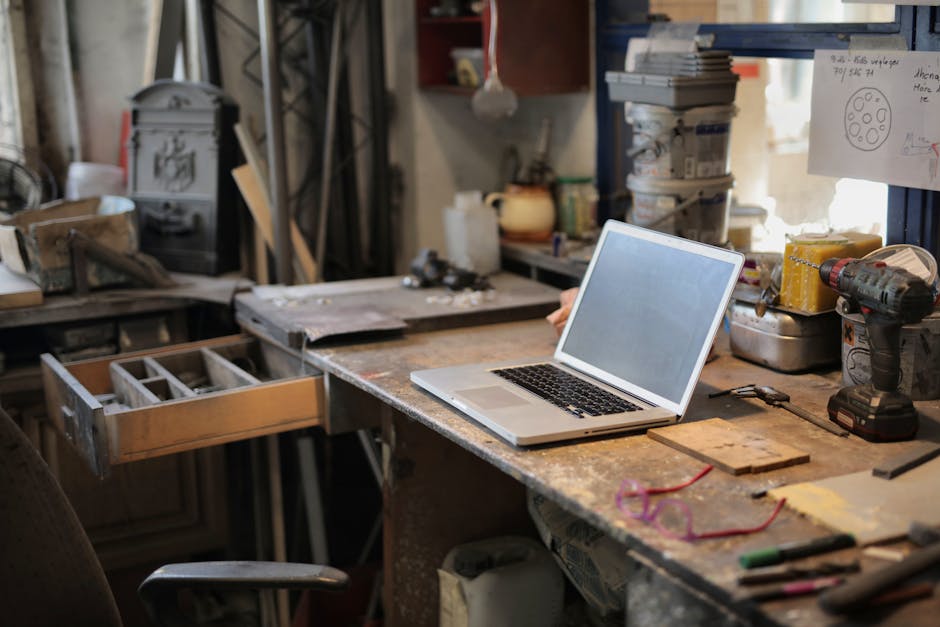
Common OSHA Violations in Manufacturing Plants
Understanding frequent violations can help manufacturers focus their compliance efforts. Some of the most common OSHA citations in manufacturing include:
- Inadequate machine guarding
- Failure to implement proper lockout/tagout procedures
- Respiratory protection program deficiencies
- Improper hazard communication
- Electrical safety violations
Strategies for OSHA Compliance in Manufacturing
1. Implement a Comprehensive Safety Program
Develop and maintain a written safety program that addresses all potential hazards in your facility. This program should include:
- Regular safety audits and inspections
- Employee training and education
- Incident reporting and investigation procedures
- Emergency response plans
2. Prioritize Employee Training
Ensure all employees receive thorough training on safety procedures, hazard recognition, and proper use of personal protective equipment (PPE). Regular refresher courses are essential to maintain awareness and compliance.
3. Maintain Accurate Records
Proper documentation is crucial for OSHA compliance. Keep detailed records of:
- Workplace injuries and illnesses (OSHA 300 log)
- Employee training sessions
- Equipment maintenance and inspections
- Hazard assessments and corrective actions
4. Stay Updated on Regulatory Changes
Given the frequent updates to manufacturing regulations, it's vital to stay informed about new or revised OSHA standards. Consider assigning a dedicated team member to monitor regulatory changes and update your compliance strategies accordingly.
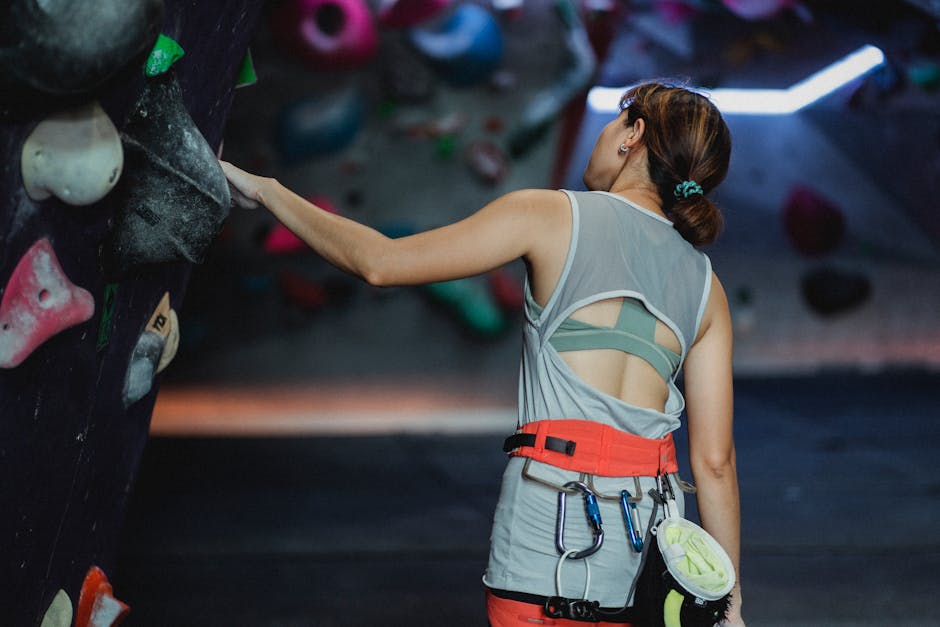
5. Leverage Technology for Compliance Management
Utilize visitor management solutions and other digital tools to streamline compliance efforts. These systems can help with:
- Tracking visitor and contractor safety orientations
- Managing employee training records
- Conducting and documenting safety audits
- Generating compliance reports for potential OSHA inspections
The Cost of Non-Compliance
Failing to adhere to OSHA regulations can result in significant financial penalties, with fines starting at $16,131 per violation and potentially reaching up to $161,323 for repeated offenses. Beyond monetary consequences, non-compliance can lead to:
- Increased workplace accidents and injuries
- Lower employee morale and productivity
- Damage to company reputation
- Potential legal liabilities
Conclusion: Building a Culture of Safety
Compliance with OSHA regulations in manufacturing plants goes beyond mere adherence to rules. It's about fostering a culture of safety that permeates every aspect of operations. By prioritizing safety, manufacturers not only avoid costly penalties but also create a more productive and engaged workforce.
Remember, workplace management plays a crucial role in maintaining a safe and compliant manufacturing environment. By implementing robust safety programs, leveraging technology, and staying proactive in regulatory compliance, manufacturing plants can create a safer workplace while positioning themselves for long-term success in an increasingly complex regulatory landscape.