Mastering Facility Maintenance: A Comprehensive Guide for Modern Workplaces
“Effective facility maintenance is crucial for any organization looking to optimize operational efficiency and create safe, productive work environments. This comprehensive guide explores the essential components of facility maintenance, from preventive strategies to technology integration, helping facility managers and business leaders implement best practices that reduce costs, extend asset lifecycles, and support business continuity. ”

Mastering Facility Maintenance: A Comprehensive Guide for Modern Workplaces
In today's competitive business landscape, the condition of your physical workspace directly impacts operational efficiency, employee productivity, and overall organizational success. Facility maintenance—often working quietly behind the scenes—plays a crucial role in ensuring that buildings, equipment, and infrastructure function optimally to support your core business activities.
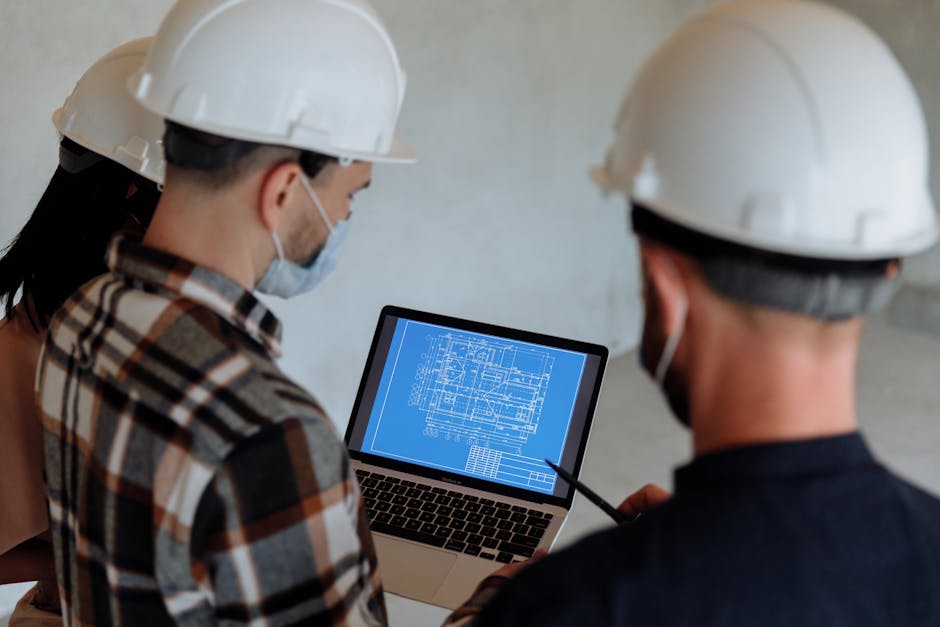
What is Facility Maintenance?
Facility maintenance is the systematic process of keeping buildings, equipment, and surrounding areas in optimal working condition. It encompasses a wide range of activities aimed at preserving assets, ensuring safety, and maintaining functionality across commercial properties.
Unlike reactive approaches that address issues only after they occur, comprehensive facility maintenance integrates preventive, corrective, and predictive strategies to maximize asset lifecycles and minimize disruptions to business operations.
The Scope of Facility Maintenance
Facility maintenance covers several key areas:
- Building Systems Maintenance: HVAC, electrical, plumbing, and structural components
- Equipment Upkeep: Regular servicing of machinery, appliances, and technical systems
- Grounds Management: Landscaping, parking areas, and exterior structures
- Safety and Compliance: Ensuring adherence to building codes, accessibility standards, and safety regulations
- Energy Management: Optimizing systems for efficiency and sustainability
For corporate HR managers, IT leaders, and facility directors, understanding the full scope of facility maintenance is essential for effective resource allocation and strategic planning.
The Business Case for Proactive Facility Maintenance
Implementing a proactive facility maintenance strategy delivers significant benefits beyond simply fixing what's broken. Organizations that prioritize maintenance planning experience:
Cost Reduction Through Prevention
Preventive maintenance typically costs 3-4 times less than reactive maintenance. By identifying and addressing potential issues before they escalate into major problems, organizations can avoid costly emergency repairs, equipment replacement, and operational downtime.
According to industry studies, every dollar invested in preventive maintenance saves organizations between $5 and $10 in reactive maintenance costs, making it a crucial component of effective budget forecasting.
Extended Asset Lifecycle
Regular maintenance significantly extends the useful life of building systems and equipment. For example, properly maintained HVAC systems can last 15-20 years, while neglected systems may require replacement in as little as 7-10 years.
Enhanced Safety and Compliance
Well-maintained facilities reduce the risk of accidents, injuries, and compliance violations. This not only protects employees and visitors but also shields organizations from potential liability issues and regulatory penalties.
Improved Operational Efficiency
Properly functioning facilities enable employees to perform their jobs without disruption. When building systems work reliably, teams can focus on their core responsibilities rather than dealing with environmental distractions or equipment failures.
Essential Components of an Effective Facility Maintenance Program
Creating a comprehensive facility maintenance program requires attention to several key components:
1. Preventive Maintenance Scheduling
Preventive maintenance involves regularly scheduled inspections, cleaning, lubrication, and minor repairs to prevent equipment failure. Developing a calendar-based maintenance schedule helps ensure critical systems receive timely attention.
Key elements of preventive maintenance include:
- Regular inspection schedules based on manufacturer recommendations
- Documented maintenance procedures for each system or equipment type
- Clear assignment of responsibilities to maintenance personnel
- Digital tracking systems to monitor completion and compliance
2. Predictive Maintenance Strategies
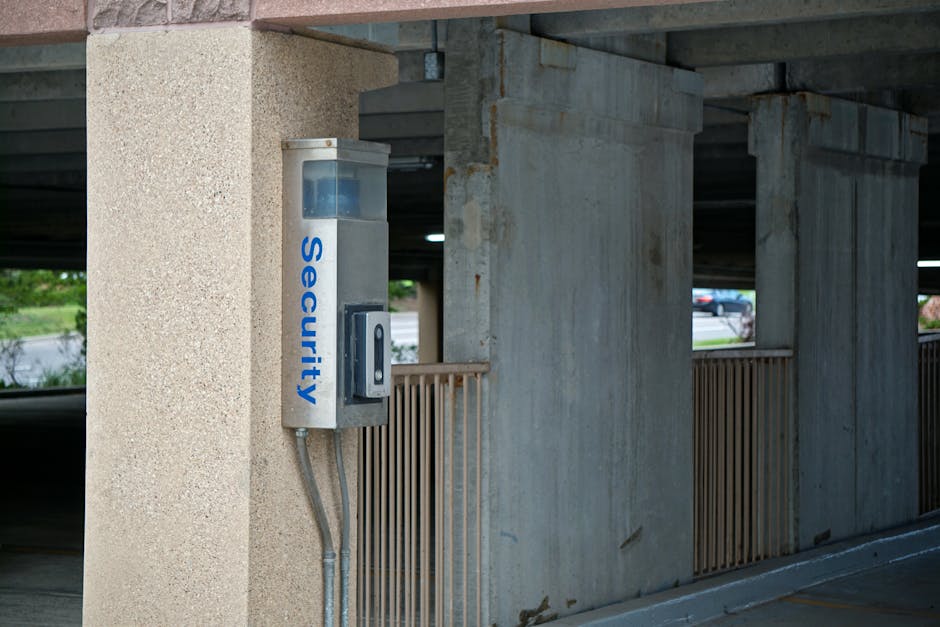
Predictive maintenance uses data analysis and condition monitoring to identify potential failures before they occur. This approach relies on various technologies:
- Vibration analysis to detect mechanical issues
- Infrared thermography to identify electrical problems
- Oil analysis to assess equipment condition
- Ultrasonic detection for air or fluid leaks
By implementing predictive maintenance, organizations can transition from calendar-based maintenance to condition-based maintenance, optimizing resource allocation and reducing unnecessary interventions.
3. Emergency Response Planning
Despite the best preventive efforts, emergencies will occasionally arise. An effective facility maintenance program includes clear protocols for addressing urgent issues, including:
- 24/7 contact procedures for maintenance personnel
- Prioritization systems for addressing multiple issues
- Vendor relationships for specialized emergency services
- Documentation requirements for incident reporting
Emergency response planning is closely tied to business continuity strategies, ensuring that critical operations can continue even during facility disruptions.
4. Vendor Management
Most organizations rely on a combination of in-house staff and external contractors for facility maintenance. Effective vendor management includes:
- Qualification and selection processes
- Clear service level agreements
- Performance monitoring and evaluation
- Coordination between multiple service providers
Developing strong relationships with reliable vendors ensures that specialized maintenance needs are addressed promptly and effectively.
5. Compliance Management
Facilities must comply with numerous regulations related to safety, accessibility, environmental impact, and building codes. A robust maintenance program includes:
- Tracking of applicable regulations and standards
- Regular compliance audits and inspections
- Documentation of compliance activities
- Remediation planning for any identified issues
Staying current with regulatory requirements helps prevent costly violations and ensures a safe environment for all building occupants.
Technology Solutions for Modern Facility Maintenance
The evolution of digital technology has transformed facility maintenance practices, enabling more efficient, data-driven approaches:
Computerized Maintenance Management Systems (CMMS)
A CMMS serves as the central hub for maintenance operations, providing:
- Work order management
- Preventive maintenance scheduling
- Asset tracking and history
- Inventory management for parts and supplies
- Reporting and analytics capabilities
Modern CMMS solutions offer mobile accessibility, allowing maintenance staff to receive, update, and close work orders from anywhere in the facility using smartphones or tablets.
Internet of Things (IoT) Integration
The Internet of Things has revolutionized facility maintenance by enabling real-time monitoring of building systems and equipment. IoT sensors can:
- Track equipment performance parameters
- Monitor environmental conditions
- Detect anomalies that may indicate potential failures
- Automatically generate maintenance alerts based on predefined thresholds
By connecting building systems to a central monitoring platform, facility managers gain unprecedented visibility into operational conditions.
Building Automation Systems (BAS)
Modern BAS solutions provide centralized control over critical building functions:
- HVAC operation and temperature control
- Lighting management
- Security and access control
- Energy usage optimization
These systems not only improve comfort and efficiency but also generate valuable data for maintenance planning and energy efficiency initiatives.
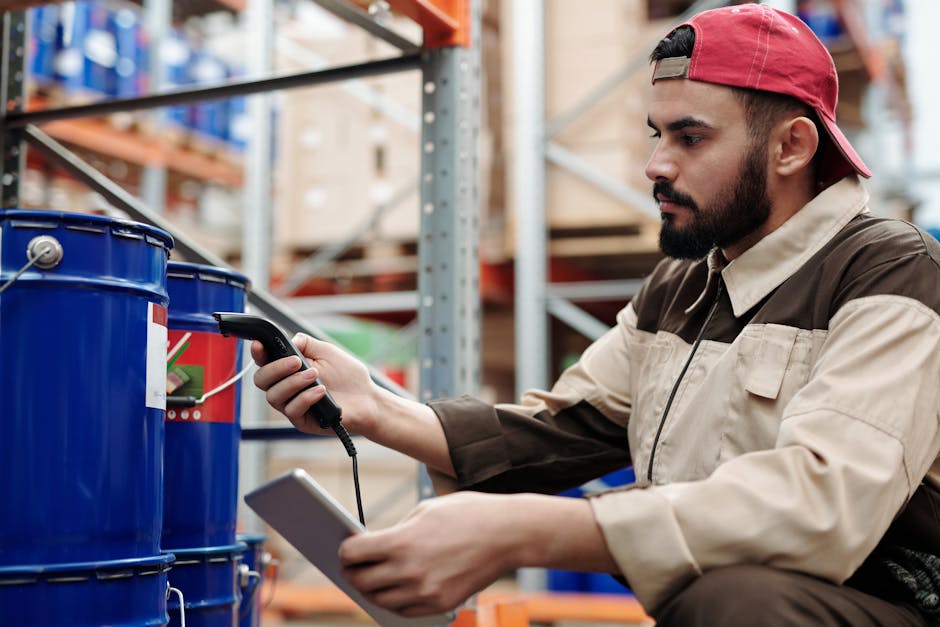
Augmented Reality for Maintenance
Emerging AR technologies are changing how maintenance tasks are performed:
- Step-by-step visual guidance for complex procedures
- Remote expert assistance for challenging issues
- Visual identification of system components
- Access to digital documentation while performing hands-on work
These tools help less experienced staff perform maintenance tasks more effectively and reduce the time required for complex diagnostics.
Implementing Effective Facility Maintenance Workflows
Beyond technology, successful facility maintenance depends on well-designed workflows and processes:
Work Order Management
A structured work order system ensures that maintenance requests are properly documented, prioritized, and tracked:
- Request submission through standardized channels
- Initial assessment and prioritization
- Assignment to appropriate personnel
- Scheduling based on urgency and resource availability
- Execution and documentation
- Verification and closure
- Analysis for continuous improvement
Effective work order management provides accountability and creates a historical record of maintenance activities for future reference.
Maintenance Documentation
Comprehensive documentation is essential for knowledge transfer and continuous improvement:
- Equipment specifications and manuals
- Maintenance histories and repair records
- Standard operating procedures
- Troubleshooting guides
- Warranty information
- Regulatory compliance documentation
Digital document management systems make this information readily accessible to maintenance staff when and where they need it.
Performance Metrics and KPIs
Measuring maintenance performance helps identify improvement opportunities:
- Mean time between failures (MTBF)
- Mean time to repair (MTTR)
- Preventive maintenance compliance rate
- Work order completion time
- Maintenance cost as percentage of asset replacement value
- Energy efficiency metrics
Regular review of these metrics enables data-driven decisions about resource allocation and maintenance strategies.
Facility Maintenance Challenges and Solutions
Organizations face several common challenges in implementing effective facility maintenance programs:
Challenge: Budget Constraints
Many organizations struggle to secure adequate funding for preventive maintenance, leading to deferred maintenance and eventual system failures.
Solution: Develop a business case that quantifies the financial impact of deferred maintenance, including emergency repair costs, premature equipment replacement, and operational disruptions. Present maintenance as an investment rather than an expense.
Challenge: Aging Infrastructure
Older buildings often have outdated systems that are difficult to maintain and inefficient to operate.
Solution: Implement a phased modernization approach, prioritizing systems based on condition assessment, energy efficiency potential, and impact on operations. Consider energy efficiency upgrades that offer attractive returns on investment through utility savings.
Challenge: Knowledge Management
As experienced maintenance staff retire, organizations risk losing valuable institutional knowledge about building systems and maintenance practices.
Solution: Implement knowledge capture processes, including documented procedures, video demonstrations, and mentoring programs. Utilize digital tools to preserve and share information across the maintenance team.
Challenge: Balancing Reactive and Preventive Work
Maintenance teams often become caught in a cycle of reactive work, leaving little time for preventive activities.
Solution: Establish clear prioritization guidelines that balance immediate needs with preventive requirements. Consider temporary additional resources to break the reactive cycle and establish a more proactive maintenance program.
Integrating Facility Maintenance with Workplace Strategy
Forward-thinking organizations recognize that facility maintenance is not just about keeping systems running—it's an integral part of workplace strategy:
Supporting Flexible Work Environments
As organizations adopt hybrid work models, facility maintenance must adapt to changing usage patterns. This includes:
- Adjusting HVAC schedules to accommodate variable occupancy
- Implementing touchless technologies to enhance health and safety
- Reconfiguring spaces to support collaboration when teams are on-site
- Ensuring reliable operation of technology that supports remote work
Enhancing Employee Experience
Well-maintained facilities contribute significantly to employee satisfaction and productivity:
- Comfortable temperature and air quality
- Reliable building systems that minimize disruptions
- Prompt response to maintenance issues
- Clean, well-kept environments that reflect organizational values
By prioritizing maintenance that impacts the employee experience, organizations can improve retention and attraction of talent.
Supporting Sustainability Initiatives
Facility maintenance plays a crucial role in organizational sustainability initiatives:
- Optimizing systems for energy efficiency
- Reducing water consumption through proper maintenance
- Implementing sustainable maintenance practices
- Supporting green building certification requirements
Maintenance teams can serve as champions for sustainability, identifying opportunities to reduce environmental impact through operational improvements.
The Future of Facility Maintenance
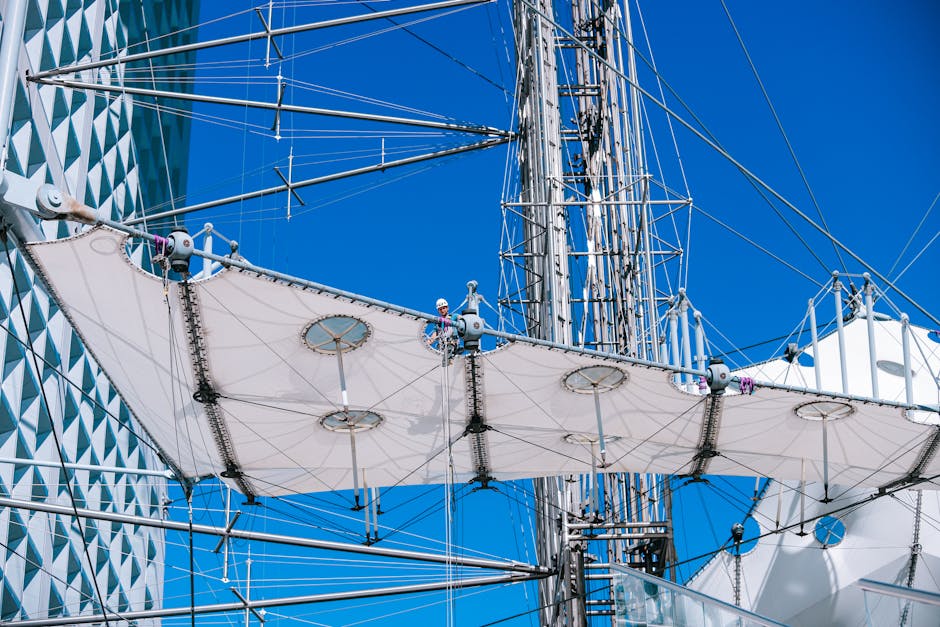
Several emerging trends are shaping the future of facility maintenance:
Predictive Analytics and AI
Advanced analytics and artificial intelligence are transforming maintenance planning:
- Pattern recognition to identify potential failures before traditional indicators appear
- Optimal maintenance scheduling based on multiple variables
- Automated diagnostics that guide technicians to root causes
- Continuous learning systems that improve over time
These technologies enable truly predictive approaches that maximize efficiency and minimize disruptions.
Integration with Space Management
As organizations optimize their real estate portfolios, facility maintenance is becoming more closely integrated with office space optimization:
- Maintenance strategies tailored to actual space utilization
- Coordination between space planning and system upgrades
- Data sharing between space management and maintenance platforms
- Joint planning for facility modifications
This integration ensures that maintenance resources are allocated effectively across the organization's real estate portfolio.
Sustainability-Focused Maintenance
Environmental considerations are increasingly driving maintenance decisions:
- Life-cycle assessment of maintenance alternatives
- Selection of environmentally friendly materials and methods
- Water conservation through proactive leak detection and repair
- Energy optimization through continuous commissioning
Organizations are recognizing that sustainable maintenance practices not only reduce environmental impact but often deliver financial benefits as well.
Conclusion: Building a Strategic Approach to Facility Maintenance
Facility maintenance is evolving from a necessary operational function to a strategic business enabler. Organizations that adopt a proactive, technology-enabled approach to maintenance can expect significant benefits:
- Reduced total cost of ownership for building systems and equipment
- Enhanced operational reliability and business continuity
- Improved employee experience and productivity
- Greater sustainability and environmental performance
- Better compliance with regulatory requirements
By investing in the people, processes, and technologies needed for effective facility maintenance, organizations create environments that support their core business objectives while controlling costs and reducing risks.
For facility managers, real estate professionals, and business leaders, the message is clear: strategic facility maintenance is not just about fixing what's broken—it's about creating and maintaining physical environments that enable organizational success.